웨이퍼: 두 판 사이의 차이
편집 요약 없음 |
편집 요약 없음 |
||
(같은 사용자의 중간 판 14개는 보이지 않습니다) | |||
1번째 줄: | 1번째 줄: | ||
Wafer. | Wafer. | ||
원래 뜻은 얇고 바삭한 과자, 또는 가톨릭 미사(성찬식) 때 성체로 쓰이는 제병을 뜻한다. 우리가 '웨하스'라고 부르는 과자도 사실 이름은 웨이퍼다. [[와플]] 역시 어원은 웨이퍼다. | 원래 뜻은 얇고 바삭한 과자, 또는 가톨릭 미사(성찬식) 때 성체로 쓰이는 제병을 뜻한다. 우리가 '[[웨하스]]'라고 부르는 과자도 사실 이름은 웨이퍼다. [[와플]] 역시 어원은 웨이퍼다. | ||
[[반도체]]의 재료 역시 웨이퍼라고 부르는데, 얇고 둥근 모양이 웨이퍼 또는 [[와플]]과 닮았기 때문. 반도체 관련 이미지에서 종종 보이는 얇고 둥근 판이 웨이퍼다.실리콘, | [[반도체]]의 재료 역시 웨이퍼라고 부르는데, 얇고 둥근 모양이 웨이퍼 또는 [[와플]]<ref>특히 아래 그림처럼 위에 칩을 올려놓으면 격자무늬가 생겨 영락 없이 [[와플]]을 닮았다.</ref>과 닮았기 때문. [[반도체]] 관련 이미지에서 종종 보이는 얇고 둥근 판이 웨이퍼다. [[실리콘]], [[갈륨]]과 같은 [[반도체]]로 만들며, 여기에 [[반도체]] 칩을 만든다. [[피자]]에 비유하자면, [[피자]] 가게에는 온갖 종류의 [[피자]]가 있지만 대부분은 아래에 깔리는 [[밀가루]] 반죽, 즉 도우는 똑같으며 그 위에 토핑을 어떻게 하느냐에 따라 [[피자]]의 종류가 달라진다. 웨이퍼는 [[피자]]의 도우와 같은 구실을 한다고 볼 수 있다. 그 위에 토핑, 즉 회로를 어떻게 올리느냐에 따라 어떤 [[반도체]]인지가 결정된다. | ||
웨이퍼의 소재로는 모래에서 추출할 수 있어서 원가가 저렴하고, 특성도 우수한 편이고 열에도 강한 [[실리콘]](규소)을 가장 많이 쓴다. 다만 고출력이 필요한 [[전력반도체]]는 [[실리콘]]만으로는 출력이 부족하거나, 발열이 너무 심하거나, [[반도체]]의 크기가 너무 커질 수가 있어서 탄화규소(SiC) 또는 질화갈륨(GaN)과 같은 화합물 소재로도 웨이퍼를 제작한다. 이런 반도체를 '화합물 반도체'라고 부른다. 당연히 실리콘 반도체보다 가격은 많이 비싸지며 특히 질화갈륨은 전력반도체로서는 성능이 좋지만 탄화규소보다도 소재 가격이 더 비싸다. | |||
[[파일:Elements of silicon wafer.png|upright 1.5|섬네일|없음|실리콘 웨이퍼 각 부분의 이름. 단, 노치와 플랫 존은 둘 중 하나만 있다.]] | [[파일:Elements of silicon wafer.png|upright 1.5|섬네일|없음|실리콘 웨이퍼 각 부분의 이름. 단, 노치와 플랫 존은 둘 중 하나만 있다.]] | ||
* 다이(die) : <del> | * 다이(die) : <del>사망</del> 웨이퍼 하나에는 여러 개의 칩을 만드는데, 그 칩 하나 하나가 차지하는 영역을 '다이'라고 부른다. 보통은 정사각형이다. 웨이퍼는 원형이기 때문에 가장자리 쪽으로 다이에 필요한 공간이 안 나오는 부분이 있으며 이를 에지 다이(edge die)라고 한다. | ||
* 스크라이브 라인(scribe line) : 다이와 다이 사이의 간격. 웨이퍼를 통으로 가공하는 공정이 끝나면 마지막 패키지 공정 단계에서 각각의 다이를 다이아몬드 커터로 잘라내는데 다이 사이에 간격이 없으면 잘라낼 때 다이가 상할 수 있으므로 간격을 둔다. | * 스크라이브 라인(scribe line) : 다이와 다이 사이의 간격. 웨이퍼를 통으로 가공하는 공정이 끝나면 마지막 패키지 공정 단계에서 각각의 다이를 다이아몬드 커터로 잘라내는데 다이 사이에 간격이 없으면 잘라낼 때 다이가 상할 수 있으므로 간격을 둔다. | ||
* 플랫 존(flat zone) : 반도체 각 공정에서 웨이퍼가 장비 안에 올바른 위치에 딱 맞게 고정되도록 원호의 일부를 잘라내서 직선 모양으로 만든 것. | * 플랫 존(flat zone) : [[반도체]] 각 공정에서 웨이퍼가 장비 안에 올바른 위치에 딱 맞게 고정되도록 원호의 일부를 잘라내서 직선 모양으로 만든 것. | ||
* 노치(notch) : 플랫 존과 비슷한 구실을 하는데, 플랫 존보다 잘라내는 공간이 적기 때문에 요즈음은 플랫 존보다는 노치를 쓰는 추세다. | * 노치(notch) : 플랫 존과 비슷한 구실을 하는데, 플랫 존보다 잘라내는 공간이 적기 때문에 요즈음은 플랫 존보다는 노치를 쓰는 추세다. | ||
==제조 공정== | |||
가장 널리 쓰이는 [[실리콘]] 소재를 기준으로, 웨이퍼를 만들기 위해서는 먼저 원통 모양의 실리콘 단결정체인 잉곳(ingot)을 만들어야 한다. 실리콘 결정은 다결정 또는 단결정 상태로 존재하는데, 단결정은 실리콘 결정이 일정한 방향으로 정렬되어 있는 반면 다결정은 결정들의 방향이 일정치가 않다. 단결정이 반도체로서의 특성이 훨씬 좋지만 만들기가 까다롭다. 실리콘을 열로 녹여 액체상태를 만들고 [[증류]]를 통해 순도를 최대한 높인다. 반도체 공정이 점점 미세해지고 있기 때문에 그에 따라 실리콘의 순도도 점점 더 높아질 것을 요구하고 있다. 이제 다결정 액체 실리콘으로부터 단결정 고체인 잉곳의 모양을 만들어야 하는데, 널리 쓰이는 공법은 초크랄스키(Czochralski, Cz) 공법으로, 도가니 안에서 실리콘을 녹이고 그 위에 종자 구실을 하는 단결정 [[실리콘]]을 올린 다음 천천히 위로 끌어올리면 용액이 종자 결정에 붙으면서 식어서 굳어 따라올라가서 단결정 원통이 만들어진다. | |||
만들어진 잉곳을 식힌 후 [[다이아몬드]] 톱으로 얇게 잘라내고 연마액과 연마장비로 표면을 거울처럼 매끄럽게 연마하면 웨이퍼가 만들어진다. 이 역시 [[반도체]] 공정 미세화에 따라 더욱 더 미세한 굴곡 없이 매끄럽게 연마해야 한다. 여기에 이후 공정에서 정확한 위치를 맞출 수 있도록 가장자리를 약간 잘라내는데, 원 모양의 한쪽을 잘라 직선 모양으로 만드는 플랫존(flat zone), 또는 원의 한 귀퉁이에 V자 모양으로 홈을 파는 노치(notch)를 사용한다. 노치 쪽이 잘라내는 면이 적어 손실도 적으므로 노치를 많이 쓰는 추세다. 일단 여기까지 만들어진 것을 베어 웨이퍼(bare wafer)라고 한다. 아무 옷도 입지 않은 <del>누드</del> 상태라는 뜻이다. | |||
흔히 150mm(6인치), 200mm(8인치), 300mm(12인치)와 같은 용어들을 쓰는데, 웨이퍼의 지름을 뜻한다. 웨이퍼의 지름이 크면 클수록 웨이퍼 한 장으로 만들 수 있는 칩의 수가 제곱으로 늘어나기 때문에 원가를 절감할 수 있지만 지름이 클수록 균일한 단결정 잉곳을 뽑아내기가 힘들어진다. 더욱 크기가 큰 웨이퍼를 만들려는 기술 개발은 계속 이어지는 중이다. 또한 웨이퍼가 얇을수록 같은 잉곳 하나에서 얻을 수 있는 웨이퍼의 장수가 많아지지만 그만큼 충격에 약하고 가공하기가 까다로워지므로 [[수율]]이 떨어지기 쉽다. | |||
==그밖에== | |||
반도체용 웨이퍼는 거의 일본 회사들이 석권하고 있는 실정이다. 극미세 공정 쪽 웨이퍼는 거의 일본 쪽에 의존하고 있는 실정이다. 2020년 시장 점유율을 보면 신에츠 27.53%, 섬코 21.51%로 일본 회사가 1, 2위를 먹으면서 절반 가까이를 공급하고 있다. 뒤이어 대만의 글로벌웨이퍼스 14.8%, 독일 실트로닉이 11.46%다. 한국에서는 SK실트론이 반도체용 웨이퍼를 만들고 있지만 아직까지는 기술 격차가 좀 있다. 2020년 시장 점유율은 11.31%로 5위다.<ref>[https://www.theguru.co.kr/mobile/article.html?no=18989 "SK실트론, 작년 글로벌 웨이퍼 시장 5위…점유율 11.31%"], 더구루, 2021년 2월 19일.</ref> 2019년 일본 아베 정부의 수출 규제 이후, 소부장 국산화 움직임에 따라 SK실트론도 미국 듀폰의 웨이퍼 사업부를 인수하면서 기술 개발에 박차를 가하고 있는 중이다. | |||
{{각주}} | |||
[[Category:반도체]] | [[Category:반도체]] |
2022년 6월 6일 (월) 03:21 기준 최신판
Wafer.
원래 뜻은 얇고 바삭한 과자, 또는 가톨릭 미사(성찬식) 때 성체로 쓰이는 제병을 뜻한다. 우리가 '웨하스'라고 부르는 과자도 사실 이름은 웨이퍼다. 와플 역시 어원은 웨이퍼다.
반도체의 재료 역시 웨이퍼라고 부르는데, 얇고 둥근 모양이 웨이퍼 또는 와플[1]과 닮았기 때문. 반도체 관련 이미지에서 종종 보이는 얇고 둥근 판이 웨이퍼다. 실리콘, 갈륨과 같은 반도체로 만들며, 여기에 반도체 칩을 만든다. 피자에 비유하자면, 피자 가게에는 온갖 종류의 피자가 있지만 대부분은 아래에 깔리는 밀가루 반죽, 즉 도우는 똑같으며 그 위에 토핑을 어떻게 하느냐에 따라 피자의 종류가 달라진다. 웨이퍼는 피자의 도우와 같은 구실을 한다고 볼 수 있다. 그 위에 토핑, 즉 회로를 어떻게 올리느냐에 따라 어떤 반도체인지가 결정된다.
웨이퍼의 소재로는 모래에서 추출할 수 있어서 원가가 저렴하고, 특성도 우수한 편이고 열에도 강한 실리콘(규소)을 가장 많이 쓴다. 다만 고출력이 필요한 전력반도체는 실리콘만으로는 출력이 부족하거나, 발열이 너무 심하거나, 반도체의 크기가 너무 커질 수가 있어서 탄화규소(SiC) 또는 질화갈륨(GaN)과 같은 화합물 소재로도 웨이퍼를 제작한다. 이런 반도체를 '화합물 반도체'라고 부른다. 당연히 실리콘 반도체보다 가격은 많이 비싸지며 특히 질화갈륨은 전력반도체로서는 성능이 좋지만 탄화규소보다도 소재 가격이 더 비싸다.
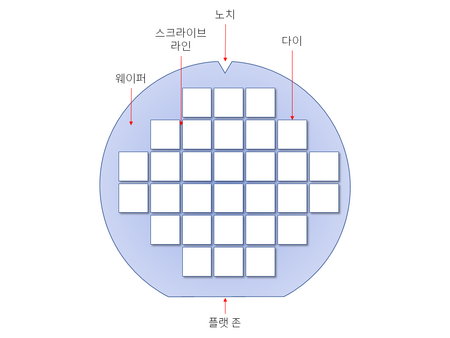
- 다이(die) :
사망웨이퍼 하나에는 여러 개의 칩을 만드는데, 그 칩 하나 하나가 차지하는 영역을 '다이'라고 부른다. 보통은 정사각형이다. 웨이퍼는 원형이기 때문에 가장자리 쪽으로 다이에 필요한 공간이 안 나오는 부분이 있으며 이를 에지 다이(edge die)라고 한다. - 스크라이브 라인(scribe line) : 다이와 다이 사이의 간격. 웨이퍼를 통으로 가공하는 공정이 끝나면 마지막 패키지 공정 단계에서 각각의 다이를 다이아몬드 커터로 잘라내는데 다이 사이에 간격이 없으면 잘라낼 때 다이가 상할 수 있으므로 간격을 둔다.
- 플랫 존(flat zone) : 반도체 각 공정에서 웨이퍼가 장비 안에 올바른 위치에 딱 맞게 고정되도록 원호의 일부를 잘라내서 직선 모양으로 만든 것.
- 노치(notch) : 플랫 존과 비슷한 구실을 하는데, 플랫 존보다 잘라내는 공간이 적기 때문에 요즈음은 플랫 존보다는 노치를 쓰는 추세다.
제조 공정
가장 널리 쓰이는 실리콘 소재를 기준으로, 웨이퍼를 만들기 위해서는 먼저 원통 모양의 실리콘 단결정체인 잉곳(ingot)을 만들어야 한다. 실리콘 결정은 다결정 또는 단결정 상태로 존재하는데, 단결정은 실리콘 결정이 일정한 방향으로 정렬되어 있는 반면 다결정은 결정들의 방향이 일정치가 않다. 단결정이 반도체로서의 특성이 훨씬 좋지만 만들기가 까다롭다. 실리콘을 열로 녹여 액체상태를 만들고 증류를 통해 순도를 최대한 높인다. 반도체 공정이 점점 미세해지고 있기 때문에 그에 따라 실리콘의 순도도 점점 더 높아질 것을 요구하고 있다. 이제 다결정 액체 실리콘으로부터 단결정 고체인 잉곳의 모양을 만들어야 하는데, 널리 쓰이는 공법은 초크랄스키(Czochralski, Cz) 공법으로, 도가니 안에서 실리콘을 녹이고 그 위에 종자 구실을 하는 단결정 실리콘을 올린 다음 천천히 위로 끌어올리면 용액이 종자 결정에 붙으면서 식어서 굳어 따라올라가서 단결정 원통이 만들어진다.
만들어진 잉곳을 식힌 후 다이아몬드 톱으로 얇게 잘라내고 연마액과 연마장비로 표면을 거울처럼 매끄럽게 연마하면 웨이퍼가 만들어진다. 이 역시 반도체 공정 미세화에 따라 더욱 더 미세한 굴곡 없이 매끄럽게 연마해야 한다. 여기에 이후 공정에서 정확한 위치를 맞출 수 있도록 가장자리를 약간 잘라내는데, 원 모양의 한쪽을 잘라 직선 모양으로 만드는 플랫존(flat zone), 또는 원의 한 귀퉁이에 V자 모양으로 홈을 파는 노치(notch)를 사용한다. 노치 쪽이 잘라내는 면이 적어 손실도 적으므로 노치를 많이 쓰는 추세다. 일단 여기까지 만들어진 것을 베어 웨이퍼(bare wafer)라고 한다. 아무 옷도 입지 않은 누드 상태라는 뜻이다.
흔히 150mm(6인치), 200mm(8인치), 300mm(12인치)와 같은 용어들을 쓰는데, 웨이퍼의 지름을 뜻한다. 웨이퍼의 지름이 크면 클수록 웨이퍼 한 장으로 만들 수 있는 칩의 수가 제곱으로 늘어나기 때문에 원가를 절감할 수 있지만 지름이 클수록 균일한 단결정 잉곳을 뽑아내기가 힘들어진다. 더욱 크기가 큰 웨이퍼를 만들려는 기술 개발은 계속 이어지는 중이다. 또한 웨이퍼가 얇을수록 같은 잉곳 하나에서 얻을 수 있는 웨이퍼의 장수가 많아지지만 그만큼 충격에 약하고 가공하기가 까다로워지므로 수율이 떨어지기 쉽다.
그밖에
반도체용 웨이퍼는 거의 일본 회사들이 석권하고 있는 실정이다. 극미세 공정 쪽 웨이퍼는 거의 일본 쪽에 의존하고 있는 실정이다. 2020년 시장 점유율을 보면 신에츠 27.53%, 섬코 21.51%로 일본 회사가 1, 2위를 먹으면서 절반 가까이를 공급하고 있다. 뒤이어 대만의 글로벌웨이퍼스 14.8%, 독일 실트로닉이 11.46%다. 한국에서는 SK실트론이 반도체용 웨이퍼를 만들고 있지만 아직까지는 기술 격차가 좀 있다. 2020년 시장 점유율은 11.31%로 5위다.[2] 2019년 일본 아베 정부의 수출 규제 이후, 소부장 국산화 움직임에 따라 SK실트론도 미국 듀폰의 웨이퍼 사업부를 인수하면서 기술 개발에 박차를 가하고 있는 중이다.
각주
- ↑ 특히 아래 그림처럼 위에 칩을 올려놓으면 격자무늬가 생겨 영락 없이 와플을 닮았다.
- ↑ "SK실트론, 작년 글로벌 웨이퍼 시장 5위…점유율 11.31%", 더구루, 2021년 2월 19일.